IOT
The Future for Industrial Services: The Digital Twin
The next big thing in industrial services will be about accurately forecasting the future of physical assets through their digital twins. Experts from GE take you behind the scene on how GE created an intelligent, IoT-based industrial monitoring and diagnostics platform that’s setting new standards.
Digitization of the industrial marketplace
The significant impact of digitization in consumer marketplaces continues to be felt through a myriad business, leadership, and technology transformations across industries such as retail, travel, entertainment, and advertising. Digitization technologies and their rapid adoption rates are at the core of globalization, which has impacted the social and political landscapes of many countries.
Now, digitization is poised to exert its tremendous influence in the industrial marketplace, and at an even faster rate than it did in the consumer marketplace. There has been an immense amount of research, alongside multiple opinion-based articles, on the digitization of the industrial marketplace. Although the actual economic value, number of connected assets, and winning ecosystems in this transformation may vary, the large financial and societal impacts that it can have remain and exceed that of the consumer impact.
In crafting their digital industrial transformation journey, GE analyzed the best approaches used by consumer marketplace leaders and leveraged the most useful ones to build upon and accelerate the journey. After analyzing key consumer marketplace leaders (such as Amazon, Google, and Apple), it was clear that they used a similar approach to sustain their leadership in their respective marketplaces. The approach was focused on a very effective pattern, which includes three essential parts:
Continually collecting a significant amount of data about each individual customer to create a model of that individual’s consumption behavior (that is, a ‘model of one’)
Implementing analytics that use the individual models to derive a business outcome and to learn from the consumption actions that are taken (that is, a ‘P&L / profit and loss of one’)
Combining modeling and analytics techniques into a platform that simplifies and accelerates their use, allowing these capabilities to be easily adapted for new services or other industry applications
This approach was used by Amazon, when it moved from selling just books to conducting general retail through Amazon Online, video and music in Amazon Prime, and then to IaaS and PaaS services in Amazon Web Services.
The Digital Twin
GE has started on its digital transformation journey, at the core of which is an approach centered on the Digital Twin. The Digital Twin collects data from its manufacturing, maintenance, operations, and operating environments and uses this data to create a unique model of each specific asset, system, or process, while focusing on a key behavior (such as life, efficiency, or flexibility). This is the ‘model of one.’
Analytics are then applied to these models to detect anomalies in the system. The twin then determines an optimal set of actions that maximize some key performance metrics, and provides forecasts for long-term planning. These modeling and analytics techniques are embedded in GE’s Predix platform and allow the enterprise to rapidly create, tune, or modify business services for customers. This is the ‘P&L of one.’
The Digital Twin is then used in a specified analytics workflow to enable the delivery of a specific business outcome, using environmental and operational data that is consistently acquired. This consistent data flow permits the Digital Twin model to continually adapt to changes in the environment or operations and deliver the best business outcome. Thus, the Digital Twin essentially becomes a living model of the physical asset or system. These twins can also be rapidly and easily scaled for quick deployment for other, similar applications.
GE has built Digital Twins of critical jet engine components that predict the business outcomes associated with the remaining life of those components; for example, of gas turbines to deliver the desired electrical power output at the lowest possible fuel consumption, and of wind turbines that collectively optimize the production of electricity from wind farms. These Digital Twins provide up-to-date and customized information that enables GE’s businesses and customers to make timely decisions and intercessions for continued profitability and maximized performance.
While the digitization efforts of the industrial marketplace are uncovering a broad span of productivity-related savings and new revenue opportunities, many of the pre-eminent early productivity benefits are being felt through the unlocking of additional value in working assets, systems, and processes. These benefits can be grouped into three broad categories: Early warning / anomaly detection, prediction, and optimization”
Early warning, prediction, and optimization
GE is using Digital Twins in the monitoring and diagnostics (M&D) space to flag irregular behaviors that could be early signs of an emerging issue. Anomaly detection systems have been in use for many decades as a means to detect possible impactful events and have been deployed at many M&D centers. Today, several Digital Twin anomaly detection models have been created that provide early warnings, which enable a potential unscheduled outage to be just a scheduled maintenance event. To begin with, these models underscore the normal or optimal behavior of the assets, systems, or processes using a consistent data flow and associated domain understanding. The domain understanding may be used to create virtual sensors from which additional data is acquired to increase the fidelity of the model.
In addition, machine learning workflows are leveraged to detect anomalies as early as possible, in order to understand if they are a precursor to a potential impactful event. GE has created Digital Twin anomaly detection models to identify anomalies in the bearings of rotating machines up to 60 days in advance, as opposed to the usual 20-30 days.
Prediction is at the core of the Digital Twin capability and leverages a combination of physics-based models and data-driven analytics to optimize key business indicators such as uptime and throughput. As an example, the Digital Twin can be used to predict the remaining life of a turbine blade on a specific aircraft engine with great accuracy. This allows the application of condition-based maintenance (CBM) to manage a specific engine, rather than wasting time with the usual periodic approach. It also determines the remaining life of the turbine blade after each flight or a set of flights, by evaluating operational and environmental data and customer needs. With this condition-based approach, the customer can determine exactly when to schedule maintenance and also take action to increase the uptime before maintenance — for example, changing filters or giving the engine a water wash to reduce contamination of key parts, thus increasing the uptime of the asset.
Industrial services are being transformed by knowing the likely outcomes of individual assets. GE has also created enterprise-scale Digital Twins that simulate full-scale, complex systems interactions, which simulate several ‘what-if’ scenarios of the future and determine optimum key performance indicators for situations with highest probability. By leveraging large data sources for weather, performance, and operations, these simulations play out possible scenarios that could impact an enterprise.
For example, power generation customers are using Digital Twins to plan fuel-versus efficiency tradeoffs so that the committed electrical power output can be delivered through minimal fuel consumption levels, or so that it can be maximized at the highest possible price. Further, railway customers are using Digital Twins to optimize a locomotive’s fuel cost and emissions on a specific trip, by processing the total weight of the train, the car configuration, the topography of the route, and the environmental conditions along the route.
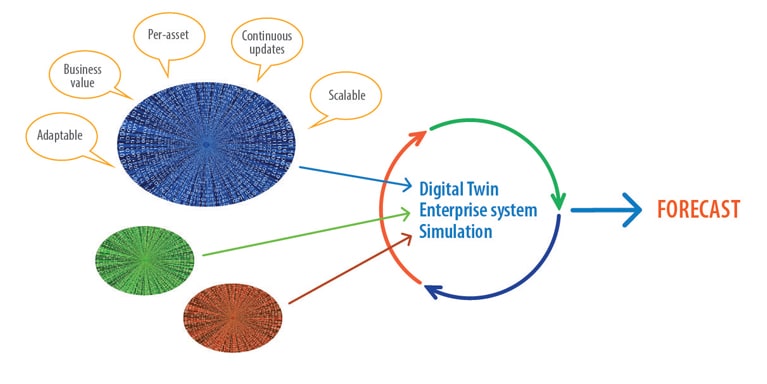
Digital Twin technologies and ecosystems
Automating model-building and scaling the Digital Twin communityEnterprise-scale simulation and optimization requires Digital Twin models of every asset, across the business portfolio. GE created the Digital Twin Framework and a companywide community of thousands of modelers to create asset-level models that become Digital Twins. The Framework hosts a variety of physics-based and analytical machine learning methods to generate models, as well as supporting infrastructure to ingest and curate data sets and to validate and publish the final models. Industrial models and analytics have precision, throughput, and other performance requirements that are substantially different from the consumer internet, and the Digital Twin Framework for GE’s Predix is the industrial strength capability for building Digital Twins.
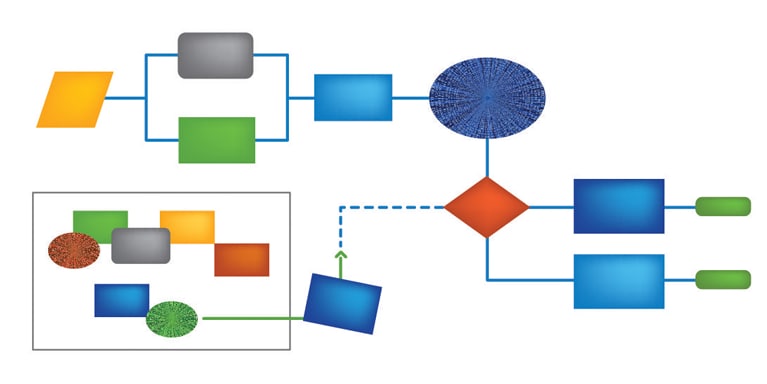
The Digital Twin Framework also provides sophisticated capabilities for building and deploying digital services applications that create economic value by optimizing over possible future scenarios. Digital Twins are published into a runtime environment built to handle the daily volume and model updates that run across multiple applications. In this environment, developers can combine the Digital Twin models with data sets and UX and UI widgets, and enable analytics to create industrial-grade applications. These applications are polymorphic, allowing users to ‘hot-swap’ analytical modules and Digital Twin models for redeployment to new applications and industries.
The Digital Twin Framework incorporates artificial intelligence agents that automatically suggest connections and insights among the model and application developers. This capability continually grows by learning from user interactions. Some of the models built in the Framework today are products of a fully automated process, learned and established from the learnings of the community and network.
Digital Twin ecosystem
The developer community is at the core of the Digital Twin. Within GE, domain experts, model developers, data scientists, and business innovators form teams that continually build new Digital Twin capabilities and outcomes. The Digital Twin Framework hosts these teams within the larger community, fostering new connections and insights as well as accidental innovation. As the framework resides on Predix, it is a resource that is available to all customers and partners. Non-GE developers and users are now growing the Digital Twin ecosystem.
Infosys is a great example of an early adopter of the Digital Twin approach. In 2015, Infosys partnered with GE to develop the world’s first Digital Twin for an airplane’s landing gear, enabling early warnings and failure predictions for several key components. This Digital Twin, combined with those of the engine, airframe, and other systems, scale to form a Digital Twin of the entire aircraft. Fuel economy is impacted by operational tradeoffs among these components — and the enterprise simulation balances these interactions to optimize fuel consumption, while also maximizing safety and timeliness. This is the power of the expanding Digital Twin ecosystem, which is transforming industrial services through its ability to forecast the future.
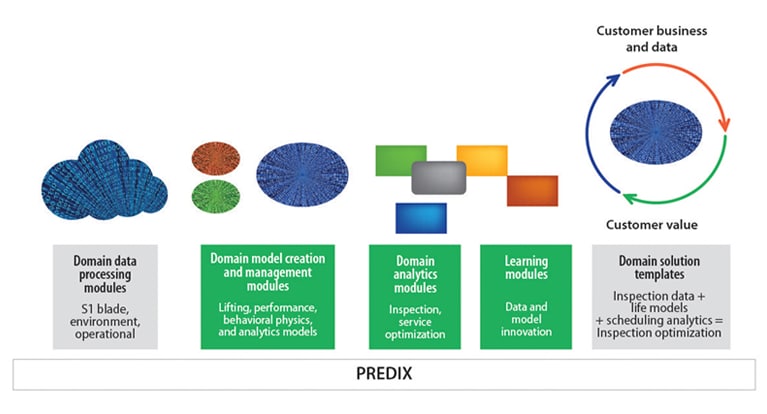
The evolving Digital Twin era
We are at the beginning of the Digital Industrial Era and the Digital Twin is in its infancy. However, we are already seeing glimpses of the tremendous changes that lie ahead. As these Digital Twins become the ‘living’ models of physical entities that they represent, they embody asset ‘memories’ and even ‘group consciousness.’ Let us consider the example of The Wind Turbine Farm — a group of wind turbines placed together that generate electricity. In this case, a wind turbines farm is deployed in a field and has been producing electricity for the past four years. A new turbine that has been in production for two months needs to be added to the farm, when suddenly its control system notices some unusual sensor input that is unrecognizable. Subsequently, the sensor in the turbine will communicate with older turbines that have been functioning in the farm and assess if they have experienced this irregular input pattern before and what events are associated with it. It might then receive inputs from these turbines that indicate that they have experienced this pattern and a potential failure event is associated with it. The new turbine then uses its Digital Twin (as it has different parts and configuration) to determine the impact on its own components. Thus, the twins are in communication and constantly learning from each other.
This notion of machines talking, reasoning, and making decisions with each other will be transformative for how industrial systems are operated and managed in the future. During the 2020-2030 decade, there may be over 50 billion machines connected together, with over seven billion internet consumers. With the network effect in play, the world will see another, even more sweeping internet transformation.