Industry 4.0 is on the boardroom agenda of every manufacturer. No executive wants to overlook it in their strategy. Leaders across industries are keen to understand Industry 4.0 and its implications to transform organizations by increasing information flow, creating new insights, and revolutionizing business models.
However, industry reports and analyst surveys provide a confusing view of the state of implementation. While forward-looking companies have made their mark in implementing Industry 4.0, a majority of them experience uncertainty when determining how to proceed and unlock measurable business value. Traditional project management approaches with standard work breakdown structures will not be sufficient for Industry 4.0 implementation. A deep fundamental understanding is needed regarding business needs and opportunities, Industry 4.0 concepts and technologies, and how they map to each other.
Challenges to scale up Industry 4.0
A closer look at Industry 4.0 reveals a powerful confluence of management trends and emerging technologies that promise to change the way factories work. Everyone agrees, the impact of this change will be unprecedented, affecting every industry in every country and transform entire product lines, production systems, business models, and service delivery formats. However, according to the 2018 World Economic Forum report The Next Economic Growth Engine: Scaling Fourth Industrial Revolution Technologies in Production, “More than 70 percent of industrial companies are still either at the start of the journey or unable to go beyond the pilot stage.” Clearly, we are still at the cusp of this revolution. So what is stopping the scaling up of Industry 4.0?
Fig. 1 Industry 4.0 and the basket of technologies
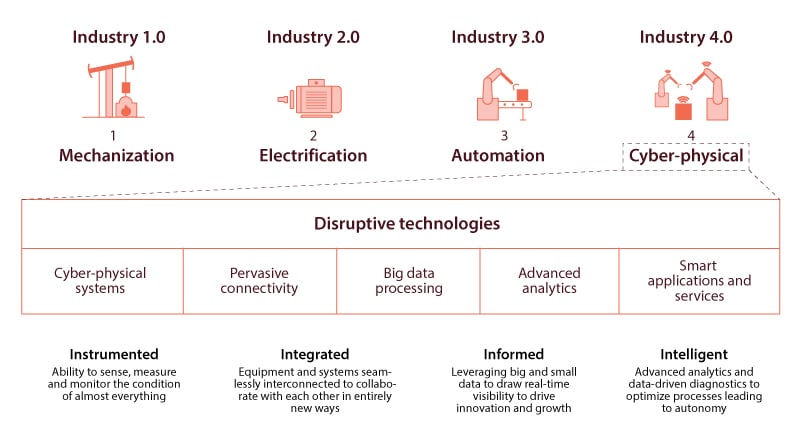
A closer look at the implementation approach will help answer this question. At the core of Industry 4.0 are cyber-physical systems, the coming together of diverse technologies, and the intertwining of virtual and the physical worlds, as shown in Fig. 1. Although the effects of this change will be seen as revolutionary when considered in retrospect, for most organizations the transformation will be a gradual one - an evolution rather than a revolution.
Industry 4.0 is not a greenfield project for most companies, unless they happen to be a digital upstart like Tesla. Technology executives need to maintain continuity with legacy systems that have evolved over the decades and are still functional.
Many enterprises have started pilots to understand how Industry 4.0 can be planned and implemented. Unfortunately, there are not many instances of these pilots scaling up to large-scale implementations, for a variety of reasons. The people element has been widely reported as a leading cause - one of the major findings from a global study conducted by Infosys in collaboration with the FIR Institute at RWTH Aachen University in Germany. While 85 percent of businesses saw potential benefits from implementing Industry 4.0, only 15 percent had a dedicated strategy in place.
A staged approach with meaningful milestones and metrics, not necessarily in strict sequence, will be preferable to a big bang. With this in mind, Infosys partnered with acatech, the National Academy of Science and Engineering in Germany, to develop an Industry 4.0 Maturity Index to provide companies a practical framework for progress. This index presents a comprehensive framework, introduced at the Hannover Messe in Germany in 2017 alongside a consortium of leading scientific and industry partners, to establish a holistic approach to translate Industry 4.0 capabilities and progress into measurable and realistic business value. It is a systematic approach for enterprises to assess their current readiness and quantify the stages of implementation, as shown in Fig 2. It shows the phases in the Industry 4.0 evolution, including broad tools and technologies in each phase. The index provides a ranking to measure Industry 4.0 capability maturity.
Fig 2. Stages in the evolution of Industry 4.0
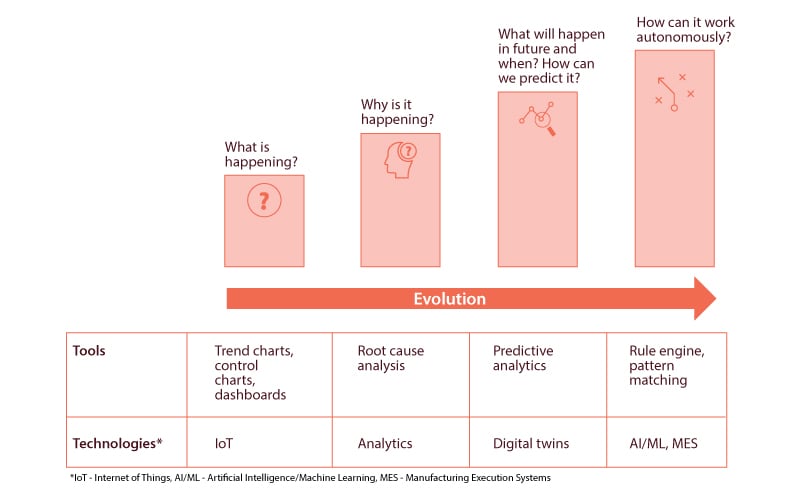
Visibility
The first phase is visibility into what is happening on the shop floor - a foundation of the Industry 4.0 journey for factories with no closed-loop system in place for ongoing feedback. Instead of being siloed and unable to communicate with the rest of the enterprise, the shop floor is integrated with other departments through an information flow.
In Industry 4.0 parlance, this phase provides closed-loop connectivity, with interoperability for systems and devices from multiple vendors and communication protocols for interacting seamlessly. Using sensors and the Internet of Things (IoT) for connectivity, vital parameters of the manufacturing system can be fed to dashboards and tools such as trend charts to monitor them.
A large food and beverage brand established real-time capture of production data from factory equipment to improve plant visibility. This initiative delivered over 50 percent improvement in line and plant effectiveness, increasing plant profitability. The transformation also eliminated up to 70 percent of manual work, including data duplication.
Analysis
Building upon the awareness of what is happening, the next question is why? Answering this question helps organizations understand the root cause behind critical incidents.
Valuable insights can be derived from raw IoT data to deduce the reasons behind events and create prediction models to identify similar problems before they occur.
In the case of an oil and gas business that produced slurry, a rotating machine that was expected to run continuously, developed issues with its moving parts and had frequent breakdowns. This created a need to predict the machine’s performance and avoid downtime. The equipment’s sensor measurement feed data was analyzed and segregated before and after a failure incident. Such analysis helped identify three clusters of data used to create a prediction model for proactive identification of failures. The initial prediction matched with the cause of the actual failure 90 percent of the time.
Simulation
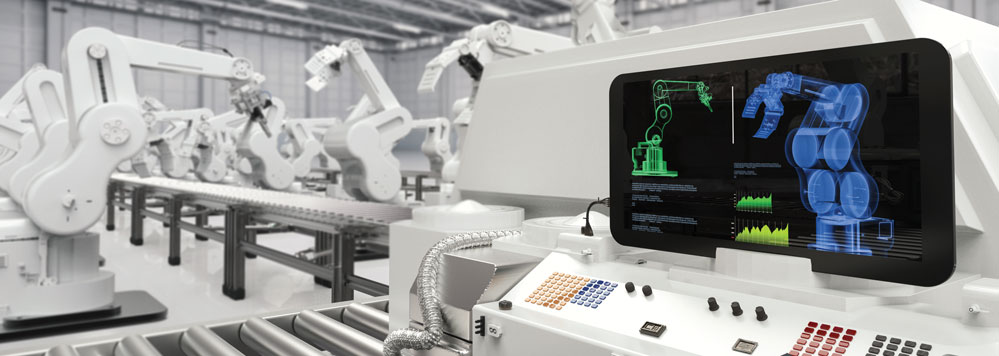
Following what and why are the how and what-if questions. Performing simulations can answer questions about a system’s state of operation under different conditions. Any signals of a malfunction predicted in the virtual system can be spotted to take timely action long before the physical system actually malfunctions.
In a digital twin project for the airline industry, a virtual model of aircraft landing gear was created to detect failure modes or potential ways in which the system could malfunction. Thirty-four sensors were placed in locations that provided data for early identification, measuring parameters such as pressure and temperature. During landing and takeoff, data was gathered once per second and fed to the virtual model. The model was then used to diagnose current issues and to predict the remaining useful life of the landing gear. This system ensured that flights operated on time and the landing gear worked without problems for the entire duration of its intended life.
Autonomous operation
The ideal Industry 4.0 system needs no human intervention; can answer a variety of what, why, and how questions; and responds proactively. Such an autonomous system leverages artificial intelligence/machine learning (AI/ML) and associated technologies.
A mining company implemented autonomous systems using AI/ML to run operations without human intervention, for improved reliability and accuracy and maximum efficiency. The systems analyzed data from diverse sources (geological, topographical, engineering, and mineralogical) to accelerate prospecting, discovery, and exploration. Sample analysis results, survey reports, and core drill data were combined to recommend mining techniques for maximum ore yield, with optimized extraction planning and execution. Robotic automation and IoT technology managed autonomous drilling systems and hauling fleets.
Enterprises at any stage of Industry 4.0 implementation must avoid the technology trap, implementing technology for its own sake, in the fear of missing out. Instead, enterprises should look at the evolutionary phases, analyze where their organization fits, and determine what business impact Industry 4.0 will offer them.
Fig. 3 Typical reaction of traditional companies to unplanned events and latency
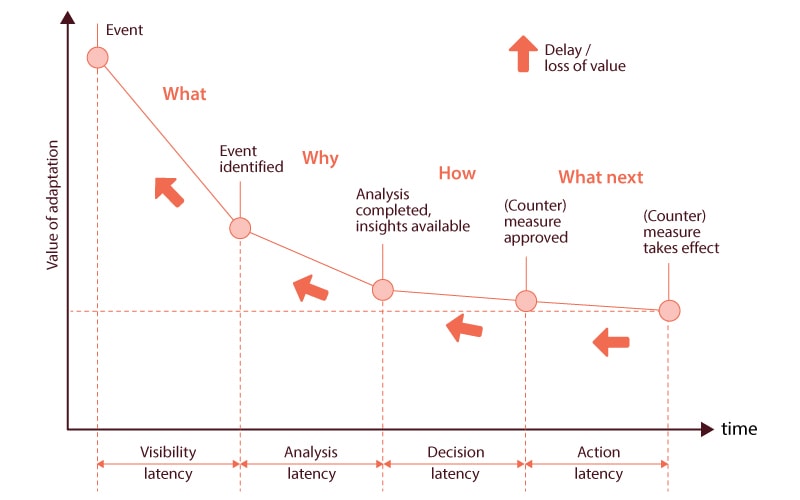
Organizations should analyze the visibility Industry 4.0 will provide: how it will generate operational insights, how undesirable incidents can be foreseen and avoided, and eventually how the system can make decisions on its own and continuously seek opportunities to secure and optimize operations - irrespective of the time of the day, day of the week, or working condition.
Industry 4.0 maturity stages translate to latency stages as well. Figure 3 shows the four latency types, stratified by a set of questions that provide a useful guide to take decisive action. Visibility latency is the time delay in identifying the issue and is transactional in nature. Analysis latency is due to the delay in properly diagnosing and evaluating the issue, and in developing an actionable root cause. Decision latency is the delay in governance and decision-making on the intervention to solve the problem. Action latency is the time taken to finish the task and complete the cycle. The approach needed for each latency type is distinct and requires a different set of actions to address the issues for that category.
Seeing the Fourth Industrial Revolution as an evolution and a progressive journey will help leaders understand their current state and develop actionable steps to move forward with confidence. This combination of bold vision and incremental progress is a practical and lower-risk means to achieve its full potential.
Adoption of Industry 4.0 with a logical approach not based on a standard template of implementation will ensure that the unique business needs of the organization are kept in mind at all stages. It will ensure that the initially defined challenges are addressed and the opportunities enabled by Industry 4.0 are achieved for maximum business impact.