The COVID-19 pandemic has amplified uncertainty for logistics companies, no matter which way they turn.
National lockdowns and business shutdowns wreaked havoc on upstream logistics chains. Container ships — scheduled months in advance — found no homes for their arriving goods. Downstream chains that include last mile deliveries are now swamped with higher volumes as consumers increasingly purchase online.
All segments of the supply chain are under pressure to adjust as markets shift quickly and in unpredictable ways. Often logistics companies look for efficiencies, but some basic elements of their business often defy solutions.
When objects fit into standard size boxes and containers, logistics companies can more easily adjust to changes in the volume of goods. However, non-uniform packages can cause delays that affect the entire shipping chain, further complicating an already difficult environment.
Large global logistics companies, such as FedEx, DHL, Maersk, and GEFCO Logistics, bill clients based on the volume of the objects to be shipped. Under normal circumstances, these companies want to place goods into as small of a box as possible to maximize space and minimize costs. However, some companies, such as GEFCO, ship a disproportionately large number of bicycles, cars, and other irregular objects. These items are either not traditionally shipped in boxes or they can require very large boxes that are not common sizes (think refrigerators and even bulkier products). The non-uniform packages present efficiency problems every step of the way: packing containers, trucks, and ships.
To offset these inefficiencies, logistics companies charge clients for space used for irregular objects. Unfortunately, clients can be quite bad at correctly measuring the objects they are shipping. This causes the logistics companies to re-measure, and then replan how to pack a container. This creates incorrect billings that must be reconciled, although that can happen with shipping regular objects too. For example, someone shipping a vase or a picture frame might estimate the dimensions of the object and miss significantly. With COVID-19, the increased volume of packages makes these scenarios much more likely, and those flawed estimates add up.
Infosys’ integrated AR app fast-tracks the remeasuring process by combining inventory management and billing systems
Technology advances, however, are giving companies new tools to manage weaknesses in the system. Infosys is creating an augmented reality application that clients and warehouse employees alike can use to more accurately measure object dimensions. Running on any smartphone OS, the integrated solution combines augmented reality (AR) with inventory management and billing systems to reduce the time spent on reconciliation and remeasuring objects.
Meanwhile, closed stores and expansion of online sales lead retailers to rely more heavily on logistics companies to deliver goods to consumers. The New York Times reported that pandemic led e-commerce is creating a shortage of delivery vehicles, with an estimated 33% more goods being shipped this holiday season.
Costs of mis-measured goods
The reconciliation process that logistics companies use to properly charge customers costs both time and money. The current method for correcting measurement mistakes uses devices of varying sizes to measure goods. Unfortunately for the logistics companies, one device can’t handle every product. One type used to measure tennis rackets aren’t useful for calculating the size of a turbine blade. Some companies offer as many as 13 different sizing models.
The process of correctly measuring goods is also time consuming, which slows departure rates and creates a bottleneck that causes fewer goods to be shipped. That’s a problem now when ports are experiencing record-setting volumes even as retail sales are lower. There is also such a strong need for shipping containers that logistics companies are sending ships back to Asia with empty containers so they do not have to unload full ones when they arrive.
Once a package is properly measured, the logistics company must still reconcile the billing difference with the client that shipped the package. When this happens frequently, this can add a large additional layer of operational support that further eats into profits with staff salaries.
How augmented reality can help
AR is not used widely in logistics yet, but it has been gaining traction in the last few years. Companies are using it to plan space in warehouses, help stock pickers save time, and replacing some paperwork. DHL Supply Chain reported that its AR glasses pilot program increased picking accuracy by 15%.
Much of these efforts, however, are still in the pilot project stages or used sporadically in most parts of the logistics industry.
Figure 1. Augmented reality on smartphones can streamline measurement.
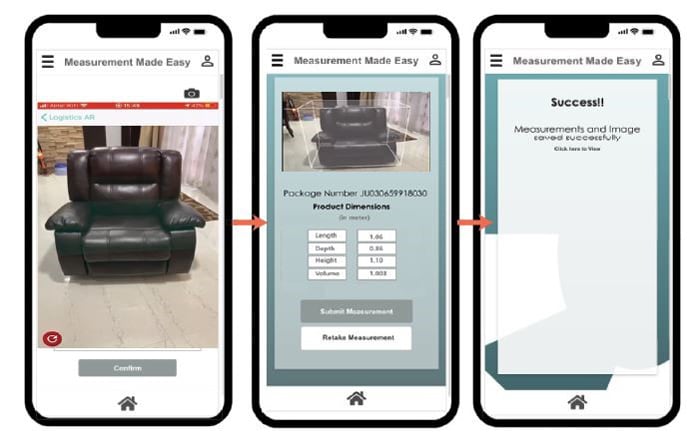
Source: Infosys
For use in shipping measurements, however, AR is rapidly maturing thanks to the ubiquity and power of modern phones. Workers might have to look around to find a tape measure, but a smartphone is almost always within reach. Their cameras and processing power can take measurements faster and more accurately than many other tools — and with minimal investment.
With Infosys’ solution, the technology can be shared with corporate clients and consumers as standard tools to ensure correct measurements in the first place. Measurement data can be captured, documented, and stored on company servers for further use. The measurements could be shared with box selection equipment to ensure the right packaging is available.
Logistics companies face many obstacles today, some of them made worse by the higher volumes being shipped. A wobbly global economy and continuing pandemic also makes predicting the future even less accurate.
That should encourage logistics companies to find solutions to problems that are actually in their control, such as speed and efficiency. In this industry, these are the elements that can make or break profit margins.