Foreword
Looking back on our time at the 2019 Industry of Things World USA in San Diego, it was an impressive combination of amazing speakers, knowledgeable participants and a highly collaborative environment. The industrial internet of things is having a tremendous impact on manufacturing. This is a foundational component of Industry 4.0 and the digital age, driving the rapid evolution of work and society globally. The opportunities for growth and success are available to all, regardless of company size or geography. Due to the proliferation of connected IoT devices in our business and personal lives, it has become more valuable than ever for leaders like you to take time from their busy schedules to share experiences and learn from each other.
As conference chair, I had the opportunity to introduce speakers from multiple industries and in multiple roles. They covered everything from digital transformation and factory of the future to how robots are changing the world to how we should educate and reskill our workforce. Along with these sessions there were numerous opportunities for attendees to connect directly with industry experts and peers to share best practices, challenges and successes. Events like IoT World USA are important as we progress through the realities of Industry 4.0.
The 2019 Industry of Things World USA was a big success thanks to the energy and contributions of the attendees, speakers and sponsors. Of course, none of it would be possible without the planning, hard work and execution of the we.CONECT team. On behalf of the Industry of Things World team and Infosys Knowledge Institute, we are pleased to present this journal that summarizes major themes from the 2019 Industry of Things World USA. We hope this journal will serve as a happy reminder of the conference for attendees and that it provides a glimpse of the expertise and insights from the event for others. Regardless of your role, we hope it will aid you on your own industrial internet of things journey.
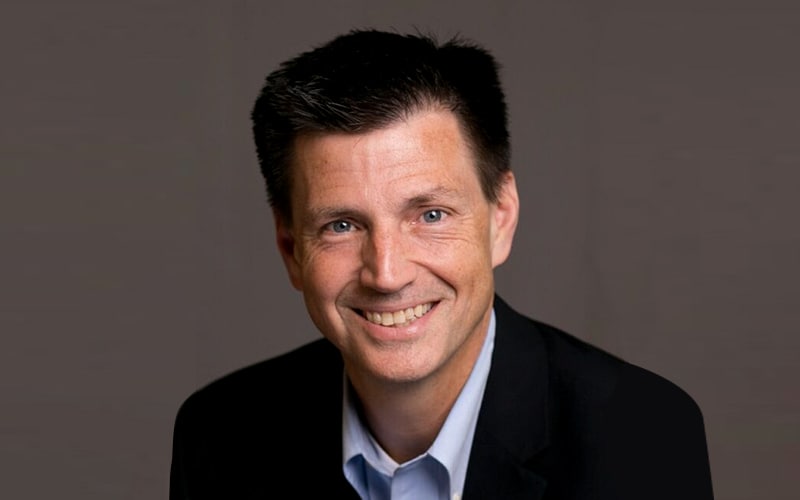
Jeff Kavanaugh
Conference Chair, Global Head, Infosys Knowledge Institute
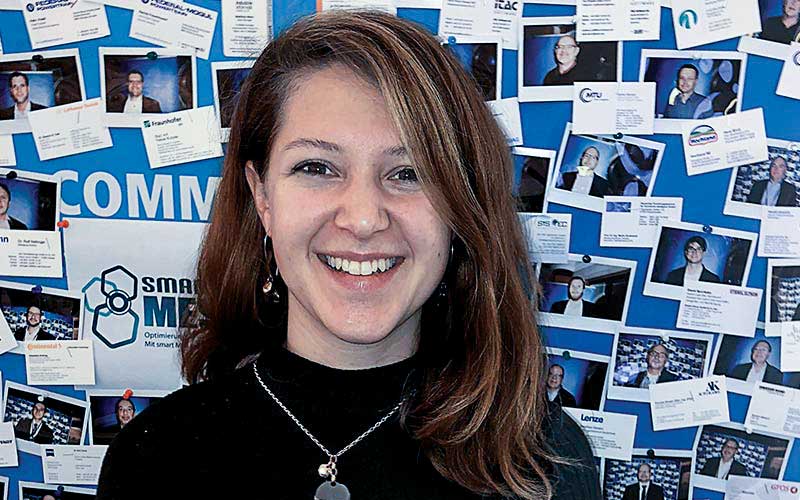
Andrea Götz
Conference Program Manager, Program Director, we.CONECT
Factory of the future
GE Appliances is a study of first movers or, more aptly put, a study of fast movers. Not long ago Haier purchased General Electric’s appliances division, and many people at GE Appliances feared that their culture would be changed for the worse. This ended up being far from the truth, according to Bill Good, the vice president of supply chain at GE Appliances. Haier’s leadership actually accelerated GE Appliances’ internet of things (IoT) journey. “Grandma’s brand, GE Appliances, is actually the fastest-growing brand among appliances in the U.S. Now, that is a bold statement,” says Good. It is also backed financially by the incremental $1 billion, 50% growth GE Appliances has experienced since the Haier purchase. What has GE appliances done to realize success in a flat market, and how has it differentiated itself from competitors?
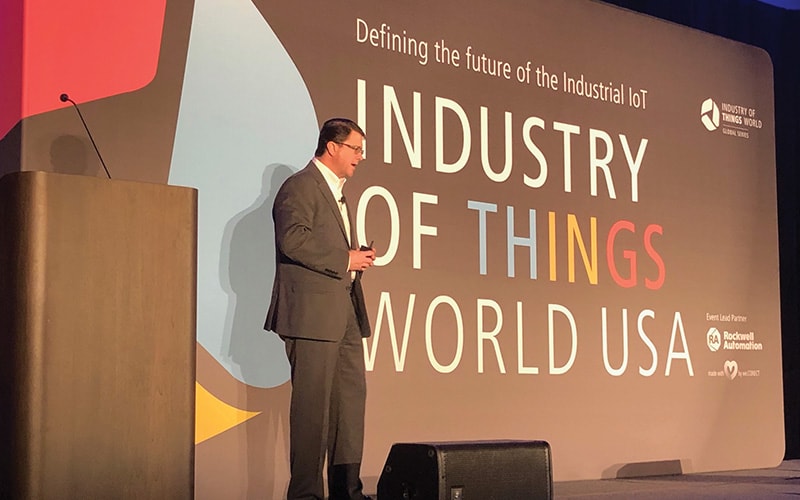
GE appliances and the market overall are faced with a new reality. Mass production is over, and we have entered a new age of mass customization. The assembly lines and mass production introduced by Henry Ford and Frederick Taylor remained much the same for more than 100 years. Of course, companies like Toyota made some modifications to reduce waste, yielding significant efficiencies. Other companies fell in line and to some extent reproduced Toyota’s lean manufacturing approach. Nevertheless, customer choice was limited, mass production design principles still held, and the efficiency improvements stretched their useful lifetime.
Now, however, we have a new generation of customers that are choosier and have higher expectations. Today’s customers want products to meet their specifications. They also want their products shipped to them in two days or less, in line with precedents established by companies like Amazon. To keep up with these customer expectations and still increase production in their appliance manufacturing, GE Appliances needed to change its manufacturing approach.
In the appliance world, GE products were seen as old and boring. As Good put it, “Our products were very stale.” Knowing that it needed to change to meet the needs of customers in this new era of manufacturing, GE Appliances decided to focus on its premium, customizable Café product line. The Café line corresponds with customers’ desire for customization. Customers can have any combination of customizations (e.g., color choice) on a range of GE Appliances products. The problem with using mass production with customizable appliances is that there is no way to create and store all possible combinations of customizations without creating significant waste. These Café appliances must be made to order as well as give customers the Amazon-like experience. There are three things GE appliances needed – things that are relevant to other manufacturers also – in order to succeed in the mass customization era:
- Data visualization
- Digital twins
- Leadership buy-in
Data visualization
In order to achieve factory operational efficiency, manufacturing professionals need to harness all the data available to them. To solve problems expediently, data needs to be captured and shared with those on the factory floor. Businesses need insight into every machine, unit, part and person if they are to attain true operational efficiency in their factories. According to Thorsten Wuest, professor at West Virginia University, Industry 4.0 is comprised of advanced manufacturing and smart manufacturing. Many companies focused early Industry 4.0 efforts on advanced manufacturing, investing in automation and additive manufacturing. Smart manufacturing, which focuses on connectivity, virtualization, and data utilization is just as important. For GE, their enterprise resource planning was their operating system, but they also used a visualization system to have end-to-end visibility into factory floor operations. Good and his team could see every unit lost, were able to monitor overall equipment effectiveness (OEE) and could run specific trend reports on nearly any parameter. Through smart boards (displays) the professionals on the shop floor finally had the insight to make a difference.
In the past, GE Appliances, like its competitors, judged its manufacturing productivity on schedule achievement. Schedule achievement assumes production lines lose 10% to 15% while still achieving 100% of schedule achievement. This is flawed. Every unit needs to be tracked with actual data, with zero loss as the ideal. Through a factory data visualization approach, GE was able to improve average ‘schedule attainment’ from 85% to 95%. Each percentage point for GE Appliances equates to $1 million per year. They even have a factory that averages 16 lost units to perfection per day at a rate of 99% to perfection over the last year. This productivity gain is due to GE Appliances having greater insight across the factory floor. Having vision into exactly where in the production line the bottlenecks or downtime occurs allows for real-time decisions and interventions that quickly address the concern.
Digital twins
Creating digital twins on the factory floor allows more insight than just knowing the product and tools. Good compared their manufacturing approach changes to moving from an 8-track player to streaming music. 3D scans of each tool and piece of machinery allows factory professionals to isolate exactly where their machine wear and tear issues occur and where bottlenecks are happening in processes. Digital twins allow for modification to manufacturing processes in a simulated but realistic environment. “Seventy percent of manufacturing costs and problems are trapped in a product’s design,” says Good. Through simulations you get a heat map of issues and areas that can be tweaked so that parts, tools, human elements and product design fit together well. Traditionally manufacturing leaders are left with intuition and guesswork about where the process needs to change. With digital twins the process becomes quantitative because manufacturing leaders have full visibility into the intricacies of their processes.
Leadership buy-in
Joe Sanguinetti, technology leader at General Mills, has also worked to improve manufacturing performance. Prior to the company’s foray into the internet of things, General Mills used a monitoring platform that cost $25,000 to $100,000 to implement on just one of its manufacturing lines. The problem with the monitoring system was that the company still had to manually find where bottlenecks were occurring in manufacturing processes.
General Mills has a mantra, “Think big, start small, and go really fast,” said Sanguinetti. If the company could justify spending $100,000 on monitoring equipment, it was worth a try to do it cheaper with IoT. The idea was to keep things super simple. Traditionally, to find out what was wrong on a manufacturing line an operator would go down to the floor and look at the stack light. “I’d probably look at the stack light and say, ‘Oh, it’s red, it’s down. It’s green, it’s running.’ Or it’s flashing, so I understand it’s waiting for an upstream or downstream action,” explains Sanguinetti. The company took this concept of monitoring the stack light and digitized it. General Mills partnered with a vendor that already does this kind of work. Now Sanguinetti and his team have insight into the precise fault that caused a machine to go down and can track the impact across the entire manufacturing process.
Sanguinetti says this project cost a total of $3,000. They were also able to install the solution from the vendor over a weekend and have it running the following Monday. “It was a quick and easy way to start playing around, and to see how you would do things differently and what that might look like,” says Sanguinetti. Now, General Mills is taking this experiment further to see how it can deploy this solution to monitor entire factories on the cloud. Sanguinetti and his team started thinking big by trying to tackle manufacturing line performance monitoring. They started small with one pilot that cost $3,000 and one weekend’s work. Now, they are moving fast to expand the pilot to the entire factory and the cloud.
Experiment and learn
Haier allowed Bill Good and his group to focus on digitization by sponsoring it. Joe Sanguinetti and his team had bandwidth and a desire to challenge their current methods of monitoring and found a cheaper digital solution. Many digital projects become vanity projects without the support of upper management and executive sponsorship. For GE Appliances, Haier set aside investment for factory digitization: They invested in order to learn and even fail in some cases. Support by Haier leadership has allowed Bill Good and his team to take risks, to test and pilot different technology to see what will work for them, and then provided additional support so that Good’s team could implement successful pilots across GE Appliances’ manufacturing landscape. While there were fears that Good and his unit would be stifled by their new owner, they have been able to grow faster than ever before. “We are growing faster than anyone else,” says Bill Good, and this is due to leadership buying into this IoT investment mindset. These tools and aids are allowing factories to truly transform during this switch from mass production to mass customization.
IoT – a different kind of data
“I’m going to be a little bit controversial today. Anybody mind?” asked Sarah Cooper as she started her presentation. Cooper, general manager of IoT analytics and solutions at Amazon Web Services, established this tone as a baseline to discuss the internet of things because she was going to challenge notions of IoT. People talk about artificial intelligence (AI) as being a brand-new technology. But AI has been around since the 1970s. “If your computer is smart, it has artificial intelligence,” says Cooper. Machine learning is what’s been missing from this artificial intelligence, but now she sees ML becoming more prevalent. Machine learning applications and devices have appeared more in physical operations. In 2018, machine learning ranked fourth as a trending technology. Now we are faced with a new technology being used in tandem with AI and machine learning – IoT. Yet data is what is most important about IoT. As Sarah Cooper puts it, “Data is really key here.”
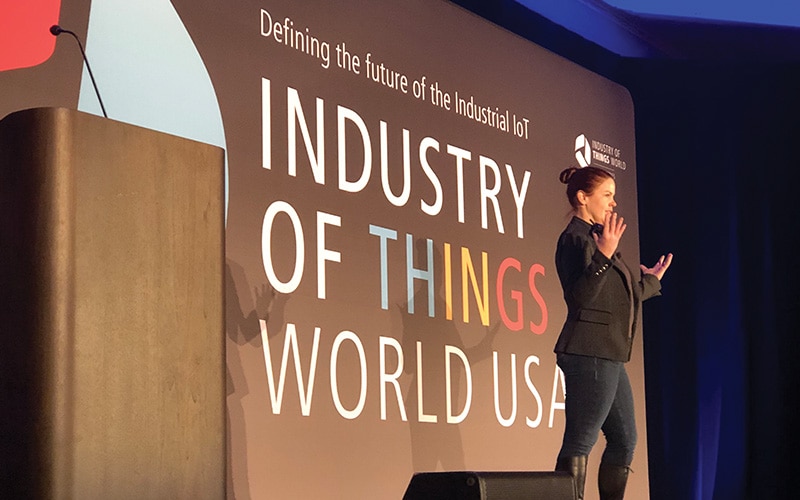
Why is data important?
As individuals we use feedback – from people, weather, body function and anything relating to Maslow’s hierarchy of needs – to make decisions in our day-to-day lives and interactions. Cooper uses the example of giving her presentation. “Right now, if this were really a connected world, I’d have a little feedback monitor right here that tells me, ‘Hey, Sarah, everyone’s leaning back and kind of to the side, about to fall asleep in their chair,’ or ‘They’re on the edge of their seats and engaged.’” As Cooper makes more active gestures, people may lean in more to experience the presentation. In this case Cooper is receiving dynamic feedback. Without this data coming from the people she is presenting to, there is no way to do the reasoning Cooper described. Without the reasoning, you cannot know the right decision to make, and without the data, you cannot develop a better control loop that drives efficiency and outcome-driven business models. “It’s the data,” says Cooper.
Machine learning on machine data is hard
Machine learning is difficult when it comes to machine data for a number of reasons. First, machine data lacks labels, situational context and relationships. Unlike application data, device data does not carry the information needed to interpret it. To solve this, context has to be built elsewhere and added to the raw data later. Second, data quality and integrity are often poor. Machine data often lacks local memory, signal processing, connection management or cheap sensor quality. Third, connected devices produce high volumes of data with sparse information. For instance, streaming terabytes of raw operations data may contain only a few kilobytes relevant to any one process or analysis. Fourth, it is difficult to distinguish deviation from variation in machine data. In the physical world, especially when humans are involved, variability is endless. Detecting meaningful deviation requires an expansive analytical toolbox. The fifth and final reason concerns high dimensionality of machine data or the high number of independent parameters in an analysis. Machine learning becomes compute expensive when working on high dimensional analysis.
In many ways data is both a blessing and a curse. While machine learning is a challenge when it comes to machine and device data, technology is growing rapidly. For the past 11 years, connected devices have outnumbered the world population. Not just the population with internet access – the entire world population was outnumbered. Today we need devices that can be updated in situ. “Innovation after installation,” says Sarah Cooper. We manufacture products for factories, not just for customers. If something goes wrong, changes need to be made in real-time without having to shut down the factory floor. Flexibility is needed in factories. Equipment that can function on every manufacturing floor and that varies from company to company needs to be able to send simple data that can be recombined and restructured in different ways, depending on how the equipment has been deployed and the specific process it runs.
Machine data context
Problems arise on factory plant floors because they are not static. For example, parts may move around for legitimate reasons, like when someone takes a pump from one piece of equipment and moves it to another. All of a sudden, OEE metrics worsen: the pump may have been moved but the data connections were left behind.
Poor data quality
“Another big challenge in this space is data quality, right? Even expensive censors periodically fail, and when they fail, they fail beautifully,” says Cooper. How about thermocouples that shoot up to 10,000 degrees, then drop negative, and then start to drift? This could be information that needs to be captured. The operator now has to identify what is valuable in all this data. Was this useful information or did a thermocouple buried somewhere deep in this two-ton machine just fail? Factory analytics must respond to ambiguous data like that presented in the previous example. Before data can be cleansed, it must be consolidated from the multiple separate technology or equipment vendors. “Typical IT vendors like Amazon like to sell to you separately,” Cooper says. Once this is done, the data must be cleaned.
To clean that data may require removing the outliers. That means only certain analytical techniques are available. Once outliers are removed, a better fit might be k-means, which are a kind of a cluster technology. However, there are certain machine learning algorithms where, if outliers are removed, that really removes necessary information.
In a related way, it is also a challenge to determine what is data deviation versus data variation that comes from machine data.
Deviation vs. variance
Typically, data scientists are brought in to solve data problems. Data scientists are just that – scientists. They are researchers, which means they come to solve the problem once. Data scientists, like k-data scientists, are not trained to think about the problem. That is the job of businesspeople. “How do we automate this? How do I have that predictive maintenance model running against 5,000 compressors on five-minute rotating intervals?” Cooper asks.
A single tool is needed, one that has been abstracted so that the analyst does not need to be concerned with the underlying data structure but instead can focus on asking the desired questions to gain understanding and achieve the performance required. In the area of predictive maintenance, a good example is the London double-decker bus. Each electric bus is producing more than 2,500 data points per second from the battery while in service. Analysts link these data points to their historical maintenance performance. They do this in order to predict battery maintenance and increase service uptime. The bus provider cannot afford for one of these buses to go down in the field. As Cooper explained, one of these buses going down means that people are missing work, not reaching their families, or any one of countless negative scenarios. AWS IoT, in this instance, helps London double-decker buses stay in service longer and ensure that maintenance is performed without having to pull buses that are in service.
Where should machine learning software run?
Run workflows where the data is. For those nervous about the cloud and worried that they will lose sales if the internet goes down – Cooper’s pointed rebuttal is “Absolutely, and guess what? The same is true in our Amazon fulfillment centers.” In order to run workflows where the data is and avoid downtime, processes need to able to be run on the edge and in the cloud. In other words, we need machine learning that is trained in the cloud and deployed on the edge. According to Cooper, three rules determine where to run workloads:
- The law of physics
- The law of the land
- The law of economics
The law of physics
The law of physics is simple and straightforward. The time in which decisions need to be made determines where the workload needs to go. You cannot move faster than the speed of light. For instance, workloads in which decisions need to be made quickly, say in milliseconds, need to be stored locally. There is no shortcut to the cloud and the round trip takes time.
The law of the land
This law pertains to where data can be stored. The law of the land complicates matters but can be distilled. If a company’s data cannot leave a facility, residency or department for regulatory reasons, a decision needs to be made. Cloud storage can be easier to manage depending on certifications and regulations. Of course, geographic location restrictions may determine that data must be stored locally.
The law of economics
This law surrounds all the costs associated with your data. Find where storing data is most efficient and effective for the company or specific manufacturing process. “It will cost you something in the round trips to the cloud,” Cooper points out. Of course it will, since storing data in the cloud means that data must be sent back. However, storing locally can create a cost problem as well. A rack is needed to store the data, and people are needed to manage that rack. As the size or data gravity increases, more rack space and more people are needed. This becomes a vertical ceiling problem: the more data collected, the more resources needed.
People need to change
As internet of things devices and output from machine learning continue to permeate our world, people will need to change their decision models. Currently people still make most decisions. There are employees who have been in their role for 30 years and can tell a machine is off just by hearing it. At the same time, there are new professionals coming into the workforce who learned through mechanical engineering courses and trained on AutoCAD. The former are challenged by digital, and the latter are digital natives. The former trust their senses, while the latter trust technology’s output. Cooper closed her session by asking, “Given all this, how do we get people to make different decisions in the face of IoT devices and machine learning?”
How robotics is changing the world
There is a lot of fear today that automation and robots are taking jobs. Many believe robots will continue to do so over the next few decades. Estimates put the total job loss to automation in the hundreds of thousands. While many jobs will cease to exist across all industries, Jeff Burnstein of Robotics Industries Association offers a counterview to the doom and gloom scenarios. Robots have not completely changed the world yet, but they are starting to change the world in miraculous ways, says Burnstein. The first industrial robot was implemented in 1961, so robots are not new. Today we are seeing what they can do in the manufacturing space.
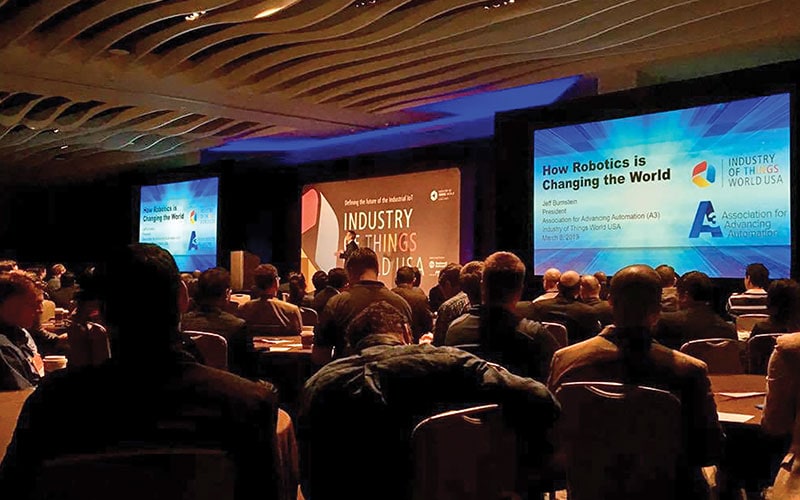
Burnstein began his work with robots at the age of 5 and has been working in the robotics space for decades with various organizations like RIA. Burnstein says:
If I would have given this talk when I first started with the association in 1983, I would have told you all these miraculous things that were about to happen. How there would be millions of robots by 1990. How they would all have machine vision. How they weren’t going to put everyone out of jobs. How AI was going to be dominating our lives and our workplaces. Any of that sound familiar? Because that’s what we’re hearing now.
Robotics is changing the world, and Burnstein covered the three major areas involved: technology trends related to the industrial internet of things, benefits of automation and workplace issues.
Robotics technology trends
Robotics implementation has been on an incline since the end of 2009 and is expected to increase tenfold by 2021. Burnstein explains that this is mainly due to implementation of industrial robots. There are two factors driving this increase in robotics adoption. The first factor is global, as everyone in the business world is trying to automate. China has made significant investments in robotics, and this is evident when considering their “Made in China 2025” plan. This plan has China not only becoming the largest user of robotics, but also the largest supplier of robotics in the world. The second trend is the idea of collaborative robots.
Collaborative robots, or co-bots, are robots that work side by side with humans in the workplace and beyond. This is a trend, Burnstein says, that is not only important for companies that already use robots but also for those that never considered using robots before, whether because robots were always seen as too expensive, too complex or only for the big companies.
Co-bots bring small and medium businesses into the automation world. “Energized by the promise of something that is easy to use and cost effective, small and medium businesses look at robotics, maybe for the first time, and perhaps they end up with a traditional industrial robot,” says Burnstein. Regardless, this trend is bringing more customers to the robotics market, such as small and medium business that would not look at robots previously.
In 2014 investment in facilities, machinery and information technology were low priorities for companies. Fast-forward to today: These areas rank as the highest priority. Why should a business leader care about these trends and growth in automation and robotics? “If you are talking about technologies like the internet of things that could add over $14 trillion to the world economy, that is a big number and big market, and everybody should care about that,” said Burnstein.
Today, Industry 4.0 work is centered on smart factories, machine learning, artificial intelligence and IoT. The key part of this new industrial revolution is to complete complex tasks and deliver superior, cost efficient goods and services. Today is about giving customers the Amazon experience, meaning that companies must give the customer what they want, how they want it and when they want it. Automation and robotics are critical steps to get that output for the customer.
The workplace – what about our jobs?
Burnstein is a Detroit, Michigan, native. He remembers Detroit being the fifth-largest city in the U.S. when he was growing up. Detroit had Ford and other manufacturers that provided jobs that made the city flourish. In 2013 Detroit declared bankruptcy, and this was largely due to manufacturers leaving the city and taking jobs with them. This mass exodus not only took production jobs but service jobs dependent on those factories, and this gutted the entire community. Housing prices plummeted and schools became ill-equipped to educate. Many jobs went to China and other parts of the world where manufacturing costs were lower. The unsettling idea was that no company could compete if it manufactured in Detroit or even the U.S. Today, however, that mindset has changed. “Now, more and more companies decide they can compete in the U.S. if they automate, and things are changing, with Detroit as a leading example,” explains Burnstein.
Detroit is one of the fastest-growing cities in the country right now. New investments are pouring into the city – some of which is for manufacturing. There is a new enthusiasm around the opportunities to manufacture in the U.S. Another IoT World USA keynote speaker, Titan Gilroy, the CEO of TITANS of CNC, described the opportunity to manufacture in cities like Detroit. There are people who need jobs and manufacturers who need employees. Titan also posed this opportunity as a win-win because not only will there be jobs, but people will have the opportunity to learn a valued skill like CNC programming. This reskilling brings productivity to these cities, and that in turn creates economic growth. Robotics has been shown to increase productivity by taking on tasks that can free time for workers to do other tasks. Predictive maintenance has shown to be one of the best early use cases for robotics and productivity improvement.
Safety
Safety in the workplace is paramount to worker well-being and long-term business success. For Burnstein and the RIA, safety has always been the No. 1 priority. Burnstein’s association developed the American National Robot Safety Standard in 1986, and it is still in use today. It safeguards the workplace by creating an environment where there is rarely a major accident relating to robotics. “But even one is too many, and as you talk about collaborative robots, working side-by-side with people, [safety] becomes a more important issue,” explains Burnstein. Risk assessments need to be done before this new working relationship can be implemented. For example, the tools a robot is holding matter. A robot with a blade can put your eye out but can do even worse with a welding gun in its hand.
Robots are making the workplace safer. This is especially true when we consider the physical jobs that they are doing. Robots are taking on jobs that require brawn and freeing up time for people to do more fulfilling jobs that use the brain. By taking people out of physically demanding jobs, robots will decrease injuries on the shop floor.
Quality and consistency
Earlier in the conference, we had an opportunity to hear from Bill Good, who spoke about quality and the need to avoid the loss of products due to defects. As Good explained, the manufacturing industry average for schedule completion is 85%, and this is not acceptable. Robotics can improve schedule completion. Robots do the same work every single day, and they make the same progress every day. When handling product fabrication, robots have the ability to create the same, consistent product every time. Along with quality in manufacturing, “robots work each and every day, making the same progress each and every day,” says Burnstein. These two factors of quality and consistency should shrink the schedule attainment gap as robotics adoption continues to proliferate.
Job killer or job creator?
Burnstein and his team at the Robotic Industries Association have created a series of videos called “Why I Automate.” He explains that once people seriously look at robotics, they have questions like “How can I automate?” “Where should I start?” and “Who can help us?” All are valid questions, but they are not the biggest concern for many. Workforce readiness is the problem people in the manufacturing world and the country at large are worried about.
“You have heard all these predictions about robots putting everybody out of work,” said Burnstein. Sarah Cooper of Amazon Web Services discussed how connected devices now outnumber the entire world population and exclaimed, “They have won!” While this was a joke, loss of jobs due to automation has instilled fear in people. This is not a new sentiment, as this fear was present at the onset of the Industrial Revolution. In 1930 the famous economist John Maynard Keynes discussed technological unemployment as technical efficiency was increasing faster than the market could address the problem of labor absorption. Burnstein takes the opposite position on this issue. He and organizations like RIA believe that robots are going to help, not hurt, employment overall. Robots will help by saving and creating new jobs, including jobs that people may never have envisioned. Burnstein investigated the issue further:
We reviewed our numbers over a 20-year period. We plotted shipments versus unemployment. What we found was amazing. Every period the industrial robot shipments went up, unemployment went down. And every period where industrial robot shipments went down, unemployment went up. Just the opposite of what you’d expect if robots were job killers.
While correlation does not equal causation, this research makes the case that robots are not job killers and we should consider the issue from a fresh perspective. Between 2010 and 2018, 177,000 new robots were introduced to the market and more than a million new manufacturing jobs were created. During the greatest period of robot adoption to date, unemployment has dropped from about 10% to below 4%. The problem is not going to be elimination of jobs. Based on Burnstein’s research, robots are job creators, or at least job enablers, as opposed to job killers.
Jobs will be replaced
Innovation has always led to the creation of new and better jobs. People have difficulty imagining the types of new jobs before they are created. Prior to the automobile, how many people would have envisioned a high-paying, specialized auto mechanic job title? In recent history, who could have anticipated the high-paying job title of iOS app developer before there was an iPhone? The current best example may be data scientist, a term and job role coined only a decade ago when data leaders at LinkedIn and Facebook used that phrase to consolidate the rapidly proliferating set of jobs with data explicitly or implicitly mentioned. Companies that have new job titles actually grow faster than those that do not. New jobs like machine algorithm designer and vision systems engineer are being created in the internet of things area. Just as innovation created jobs in the past, it will continue to do so. The workforce is not endangered; instead, it will likely be energized.
Automation on its own has created a net total of more than 60 million new jobs. Not eliminated, but created. The world is changing quickly, driven partially by the new IoT technologies. The question now is whether the workforce is ready. The World Economic Forum released studies that reaffirm the idea that more jobs will be created than lost. However, these studies also illustrate a skills gap that will only continue to widen if not addressed aggressively.
Manufacturing production training: Stop talking and start doing
Jeff Burnstein spoke at length about how robots and automation are actually creating more opportunity, not taking jobs away. Jobs at risk are those that involve manual skills or precision-based, in areas like quality control and maintenance. New jobs require skills like analytical and critical thinking, creativity, and emotional intelligence. Estimates from the World Economic Forum indicate 75 million workers will be displaced through automation. At the same time, WEF estimates that automation will create 133 million new jobs. Who will perform these new jobs? With the need for manual skills on the decline, how can people learn the skills needed for new jobs? Titan Gilroy, CEO of TITANS of CNC, is not afraid of this skills gap. However, he does believe we all need to take an active role in reskilling the U.S. workforce.
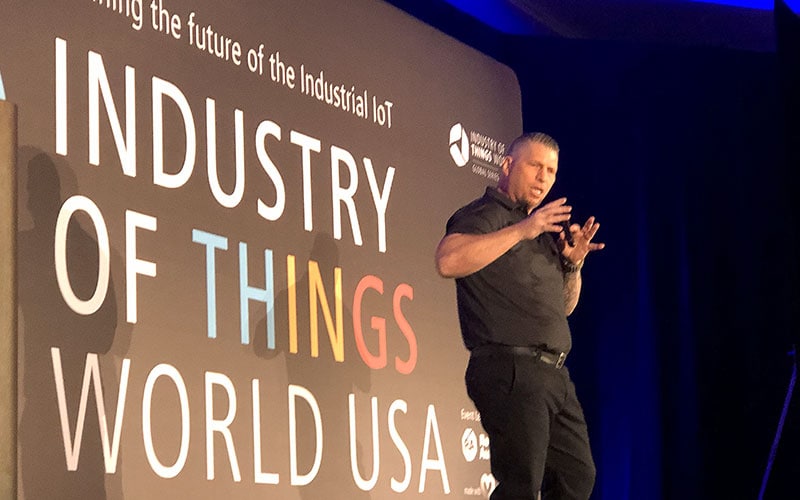
Titan Gilroy projects a powerful presence, commanding the stage and getting his message out through an outsize social media presence. His company, TITANS of CNC, has achieved great success in manufacturing by working with aerospace companies like SpaceX, Blue Origin and Boeing. While the business results are impressive on their own, Gilroy also has a perspective on what needs to be done to bridge the knowledge gap and develop a new generation of makers in the U.S. This sentiment is shared by others such as Jeff Burnstein of RIA, who said, “The skills gap is real and is having an impact.” Like Gilroy, Burnstein believes we need to bridge this gap and find ways for everybody to benefit. Gilroy, through his company, has already started this mission.
Gilroy is a leader in the manufacturing industry for computer numerical control systems. He was once a formidable boxer, and he has turned his fighter mentality from boxing to advocating for American manufacturing. In the 2008-2009 downturn, Gilroy, like many others, lost his small company. Times were hard and companies in the U.S. outsourced work to decrease costs and compete with the so-called China price. At the same time, machinists were aging out of the industry quicker than they were being replaced.
The problem, Gilroy identified, is that there is no action to close the skills gap. Year after year and conference after conference, people have talked about the skills gap. Professionals speak about how people in manufacturing are retiring and kids do not care about manufacturing. Gilroy expands:
It is spoken about so many times without action. Then we just keep talking about it without actually bringing a solution. We can talk about other countries in this information age where that’s happening, and we can talk and talk and talk and try to raise money, but if we don’t actually learn how to plant fields, if we don’t actually learn how to teach the people, if we don’t actually come in with a solution to the problem, then it is just going to be talked about forever with no results.
Kids are talked about a lot today in a negative light. They are perceived as lazy, spending too much time in front of screens and not working as hard as today’s adults did at their age. People do not realize that kids have grown up on the technology that is at the center of automation – computers. Yet manufacturing programs today typically teach them manual processes before the student is ever allowed to touch a computer because that is how it was done previously. Instead of building upon familiar skills, trainees have to essentially start from a new, uncomfortable place. “You lose them, and then you complain about it,” says Gilroy.
Education is broken and a solution is needed
The U.S. ranks 27th in education worldwide. “You want to know what we rank first in? Incarceration,” Gilroy states. Today, when people get out of prison they are likely to go back. This is because many come out of prison without marketable skills, they cannot get a job, they commit criminal acts and the cycle starts over. Even with big budgets for education, like in California, recidivism for felons is still high. Due to Gilroy’s unique past as an ex-convict who has achieved great success, the state of California asked for Gilroy’s help. “I went in and built my own type of school,” said Gilroy.
Gilroy created a CNC education program through his work with the California prison system. Instead of learning machining through manual processes and then getting on the computer, he flipped the script. He started by designing parts on the computer, then programming the CNC machine and having students mill the part. This system is designed so that students get to know the processes and the parts intimately. What makes this program special is that it is completely free. All one needs to start learning is an internet connection and a machine. “Horizontal mill usage in plants is up 700%. Who’s teaching skills for horizontals? Who’s teaching how to actually make up a million parts and make the machines dance on their own while you sit over there and have some coffee? Nobody,” says Titan.
His program has reached people all over the country. Mark Davis is a lecturer at the National Technical Institute for the Deaf, and he learned of TITANS of CNC while investigating new programs for his students. Davis teaches his students to make chess pieces with CNC machines. Gilroy met with Davis and realized he as well as his students were deaf. Through Gilroy’s CNC program, Davis was able to teach deaf students to work with CNC machines. Five of Davis’ students graduated recently and are working in high-end manufacturing.
Many schools have purchased 5-axis machines, yet the equipment remains idle because there is no standard curriculum. When English, math, biology and other subjects are taught, there is a standard, but this is not the case for CNC. Gilroy and his team are developing a standard curriculum for a number of machines including complex 5-axis systems. Gilroy’s CNC programs also teach students how to make parts that are used by the same rocket companies Titan supplied in his previous company. The manufacturing industry will continue to grow, and it is imperative that professionals in the industry take an active role to educate the next generation of workers.
Bring it in-house
Throughout the conference, many ideas and perspectives were shared. A consistent theme was using automation as a catalyst to bring jobs back to the U.S. Automation will improve our ability to compete on a global scale. Automation will allow manufacturers to make parts cheaper, faster and better. According to several prominent attendees, the first step is to build a qualified workforce through standardized education programs. The programs Gilroy and his team created and implemented were held up as role models for others.
Next, use the educated and skilled workforce in automation tools like CNC to bring companies back to the U.S. Not only will education bridge the skill and workforce gap in manufacturing, but it can also reinvigorate cities like Detroit, Chicago and Oakland. Gilroy designed a mock manufacturing plant that would cost $20 million to build. He made the case that while there are billions of dollars in manufacturing opportunities, it costs only $20 million to create a small modern plant to improve cities like Detroit. He believes this can generate momentum and perhaps even save an entire city, and then inspire other cities to follow suit. “Manufacturing can solve these problems if we get serious about it,” says Gilroy.
Digital transformation with 5G
In the past 20 years, the world has gone through tremendous change. With the advent of 3G and 4G, more people than ever before have been connected. Yongbin Wei, senior director of engineering at Qualcomm, shared his view: “I think global mobile platform devices are probably now at the 8 billion level. With something like 7 billion human beings, we actually have more than one device per human.” Wei has more than 200 U.S. patents and leads new technology development at Qualcomm including 3G, 4G LTE, and recently 5G New Radio technology for industrial IoT and spectrum sharing.
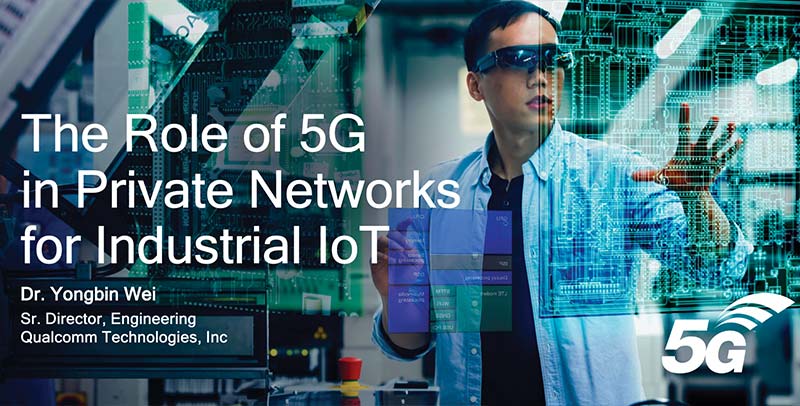
Now that humans are connected through their mobile devices, with the creation of 5G people are trying to connect everything else. This includes all sensors, cars, thermostats, and wind farms and any other device that you can envision. The total impact of 5G global production is estimated to be $12 trillion by 2035. That is an exceedingly large number for only being about 15 years away.
5G components
5G is the fifth generation of mobile connectivity and is meant to go beyond just connecting people. 5G will continue to support mobile broadband like smartphones but will also begin to create new services. 5G will address mission-critical service, and this type of service is new to the industry. Traditionally the industry has been concerned with services to consumers known as fast effort. When a consumer connects to the web, it may take a few seconds, and the consumer may not be happy, but the connection will still occur after some time. Mission-critical service, on the other hand, has stringent time and accuracy requirements, meaning that not meeting them will result in failure for business operations or something even worse if human safety is at risk.
Another important element of 5G is the spectrum, which is essentially the lifeblood of wireless communication. The spectrum in both 3G and 4G is in the lower and middle bands below 2.6 gigahertz. “Obviously, as we pump more and more data into the network, your turnpike becomes crowded, so we need more spectrum,” says Wei. 5G moves up in frequency band, to 20 gigahertz, 40 gigahertz and even 60 gigahertz.
The last component of 5G is deployment models for connectivity. Today we have what are referred to as wide areas of networks. “Wide area networks” means just that – networks that cover large areas. These are the cellular towers that can be seen from the highway and in cities. However, with the new services businesses are looking to create, network coverage will need to be more localized in factories, the office or shopping malls. As 5G progresses in connectivity, wide area networks will still be created, but there will also be a greater diversity in local networks.
While one part of the 5G vision is going beyond connecting people to connecting things, the second part is optimization. That means optimizing the 5G system to support vertical industries. “The vertical industry could be automobile, smart manufacturing or other things, and that is the plan for the coming years,” says Wei. Customized production and manufacturing will be realized through the combination of Industry 4.0, 5G, wireless and increased computing power.
Factories unchained
Currently, factories have massive amounts of cable throughout their facilities, and this makes customization difficult. To move components in a manufacturing line, you also have to move the wires and network connections. The future of manufacturing requires flexibility and elasticity on factory shop floors in order to keep pace with rapidly evolving customer and business demands. While moving cable-connected equipment is cumbersome, wireless networks give factories needed flexibility to move equipment and processes around without losing connections. The wires are there, but they are virtual and invisible.
Private networks
Early in the 5G cycle, corporations have begun to design their own private networks, primarily for privacy and reliability. A private network allows optimization for specific factory operational aspects, and is fully dedicated and not in competition with other devices like smartphones. Since these networks are local and private, they are also secure. However, there are challenges when designing one of these networks within a factory environment. Radio frequency waves do not like metal. In our daily lives, metal typically does not cause issues, but factory environments are riddled with metal. Machinery, tools, robots and so much more can interfere with frequency and create blockage.
Network blockage is unacceptable when delivering mission-critical services. Wei and his team have been working on the blockage problem for factory environments, and the current solution is signal diversity, or redundancy. Signal diversity ensures that if signals get blocked, there are still multiple other signals that maintain the connection to the network.
The second challenge is to integrate the 5G networking system with industry ethernet. Ethernet was created many years ago, but the industry has taken that as the baseline and optimized it to support deterministic low-latency, low-jitter traffic, which can be used to control motion and machines. The marriage of industry ethernet and 5G is another area technology providers like Qualcomm are trying to resolve. One potential solution could be a 5G adaptor, allowing companies to leave their current investments, such as machines and servers, in place while extending 5G capabilities to the network as a whole.
Spectrum
To get service today, operators go to a regulator and get licensed spectrum, and then deploy their network. This will continue to be the case as 5G proliferates, but factory owners can also deploy their 5G networks through unlicensed spectrum. In the U.S., the Federal Communications Commission has a spectrum that operates at 3.5 gigahertz. This is primarily used by the military, but anyone can use it as long as they meet certain requirements. This is more of a shared spectrum that can be used by different entities within the same area. In Germany this is already done for industry operational use. However, there are reliability concerns: Because it’s unlicensed, anyone can use it.
Unlicensed spectrum may not be indicative of whether service is reliable. Service reliability will depend on system design and network deployment. An example is hotel Wi-Fi, which bogs down when too many people use the service. In a factory operation, you have control of who can get into your operation. Factories can design their systems as secure isolated environments and block interference. This enables high-quality service while using an unlicensed spectrum.
Moving forward
Over the next year, companies will release the first versions of 5G devices, systems and networks. Wei and his team at Qualcomm are already seeking ways to optimize 5G for the industry overall as well as specific use cases, and in the process gathering many requirements. They are concerned with supporting services such as ultrareliable low-latency, marrying the industry ethernet with 5G, and providing operators more options to find spectrum to use and deploy their services. Providers are working ahead of 5G deployment to ensure factory operators can begin to utilize 5G as soon as it is available and that it has enough flexibility to meet the demands of every factory operator.
Contributors
Infosys would like to acknowledge the contributions made by each of the speakers who contributed to this journal. Their insights and thought leadership are greatly appreciated and helped make Industry of Things World USA 2019 a richer experience for all participants.
Bill Good
Vice President Supply Chain, GE Appliances
Joe Sanguinetti
Technology Leader, General Mills
Dr. Sarah Cooper
GM IoT Solutions, Amazon Web Services
Titan Gilroy
CEO, TITANS of CNC
Jeff Burnstein
President, Robotics Industries Association
Yongbin Wei
Sr. Director of Engineering, Qualcomm Inc.
Thorsten Wuest
Professor, West Virginia University
In addition, we would like to thank you the other 50+ session leaders, as well as the other experts who contributed to Industry of Things World USA 2019 and made it an inspiring experience.
To learn more, please visit industryofthingsworld.com.
About Infosys Knowledge Institute
The Infosys Knowledge Institute helps industry leaders develop a deeper understanding of business and technology trends through compelling thought leadership. Our researchers and subject matter experts provide a fact base that aids decision making on critical business and technology issues.
To view our research, visit Infosys Knowledge Institute at infosys.com/IKI