Insights
- The process industry is highly efficient due to its continuous manufacturing with large economies of scale but with high financial impact in case of any disruption to operations.
- The chemical industry under process manufacturing has been the second largest US manufacturing sector measured by value added in the period 2005-2022.
- Industry 4.0 will play a key role to mitigate the risk of disruptions and achieve the process industry’s operational targets.
- Companies in process manufacturing should assess where they are in the Industry 4.0 maturity with an index and set a time-bound target of what higher level to achieve when.
- The stages in the maturity of Industry 4.0 adoption and their basic tenets should be mapped to specific business objectives.
The chemical industry has been the second largest US manufacturing sector (after computers and electronic products), measured by value added in the period 2005-2022. It supports more than 25% of US gross domestic product with its supply of raw materials across industries. Process manufacturing includes products such as chemicals, oil and gas, paint, food and beverages, and pharmaceuticals.
The chemical industry, like the broader process industry to which it belongs, is highly efficient due to its continuous manufacturing with large economies of scale. However, production stoppages —whether planned or unplanned —cause disproportionally high financial impact.
The chemical industry, like the broader process industry to which it belongs, is highly efficient due to its continuous manufacturing with large economies of scale
In the oil and gas industry, the hourly cost of plant downtime doubled in 2022 to $500,000, primarily due to oil price inflation and stressed supply chains. The total cost of annual unplanned downtime per plant increased to $149 million due to penalties for late product delivery. On a positive note, the average hours of unplanned downtime per month fell from 32 days to 27 days due to digitization and preventive maintenance efforts.
Industry 4.0, characterized as the Fourth Industrial Revolution, comprises broad digitization across enterprises, specifically within factories. It has four technology-agnostic tenets and a basket of associated technologies for each tenet, building upon each other with increasing complexity and business impact. From basic sensing, Industry 4.0 progressively implements closed-loop analytics to identify actionable insights from the sensed data, simulates scenarios, and culminates with autonomous decision-making at its apex. Artificial intelligence (AI) including generative AI is at the highest level of complexity and maturity in Industry 4.0 adoption with the most business benefits. Generative AI will play a key role in operating profitability in process manufacturing plants across sectors.
Industry 4.0 maturity index
The four broad tenets of Industry 4.0 are 1) interoperability for assets to talk to each other; 2) real-time capability or technical assistance for rational fact-based decision-making; 3) virtualization or information transparency to simulate situations, and 4) decentralized decision-making with autonomy.
Industry 4.0 initiatives in process manufacturing are niche, specialized applications specific to the sector. Infosys has developed an Industry 4.0 maturity index in collaboration with partners. As with the broader definition and application, using AI is also the most advanced level in the maturity index.
Industry 4.0 has a basket of digital technologies to be applied, depending on business needs. One approach for Industry 4.0 journeys is to consider existing investments and the required implementation plan for a roadmap, based on maturity levels. Infosys has been part of a collaboration with Acatech, the German National Academy of Science and Engineering, and other partners, to come up with a framework for the maturity level of industries.
The following are the four levels of maturity with increasing complexity (Figure 1):
- Visibility — When the organization knows what is happening, measuring key parameters with sensors and the internet of things (IoT).
- Transparency — When we know why certain key events happen, by using analytics to conduct root cause analysis for uncommon happenings.
- Predictability — The capability to simulate situations and conduct what-if analyses with digital twins and associated technologies.
- Adaptability — When the system can autonomously make decisions without human intervention, using AI.
Figure 1. Industry 4.0 maturity levels in adoption
Source: Infosys
Aachen University and Infosys conducted research on Industry 4.0 in the process industry and developed a maturity index tailored to process requirements. The complexity of this industry presents additional opportunities to be more responsive by blending technology and processes to optimize production in line with the four Industry 4.0 maturity levels.
IoT and analytics
Implementing IoT with sensors and networks is the basic maturity level in the Industry 4.0 journey (see Figure 2), for visibility. However, although a significant number of manufacturers have invested in IoT - 62% have adopted IoT in 2023 according to one study - IoT, they have not realized the full business potential of using IoT sensors in this way. Fewer than 60% of manufacturers in the above study have realized real-time visibility to their assets, a key benefit of IoT. Analytics plays a crucial role to derive valuable and actionable insights from IoT data. ExxonMobil collects 6 trillion data points using IoT sensors from its refineries and chemical plants. Using analytics, this data drives efficiency and reliability at its sites, in addition to potentially reducing emission levels.
Figure 2. Digital technologies for Industry 4.0 with increasing levels of maturity
Source: Infosys
Simulating petrochemical operations
Predictability is the next level of maturity in Industry 4.0 beyond visibility. A leading North American petrochemical manufacturer used simulation technologies to evaluate its critical equipment and mitigate downtime due to either failures or essential maintenance.
Plant shutdowns last for multiple days, and maintenance engineers take months to plan for it and source spare parts, seeking to minimize each precious minute of downtime. They assess the remaining life of the equipment along with safe and efficient operating limits, so that the equipment does not fail between maintenance periods.
Another petrochemical refinery focused on its heat exchangers, critical components that account for up to 30% of the capex. To manage this, the manufacturer partnered with Infosys to use historical data to simulate the use of heat exchangers. The solution also used machine learning (ML) to estimate corrosion in heat exchangers, again leveraging historical data to deliver actionable insights.
The processed insights are delivered through an app, integrated with the manufacturer’s asset performance management platform. The pilot results encouraged the plant to scale the solution to all heat exchangers. The manufacturer expects that once this simulation approach is fully integrated across the 25 critical heat exchangers, their life will be extended by between five and 10 years, with a $1.5 million annual savings in operating expenses.
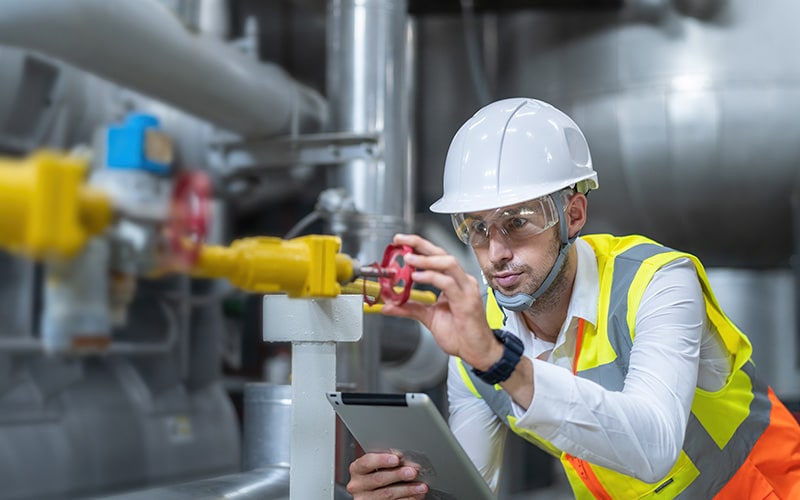
Digital twins to optimize production
Digital twins can mirror the performance of assets in real time using mathematical models and data feeds from IoT-enabled physical assets. A study found 44% of manufacturers have implemented digital twins in 2022, with another 15% planning to do so.
A pharmaceutical company in Europe sought to optimize its cell culture process to manufacture vaccines. The company wanted to monitor the process remotely, predict cell culture behavior, and gamify the app to incentivize factory employees to undergo operational training. A digital twin of the process captured real-time data using sensors and made them accessible using a digital twin app on mobile devices. A 3D visualization of the entire plant provided a virtual experience of walking through the plant. The digital twin app gave the potential to predict batch results from the third day of the culture process, instead of being reactive.
AI for autonomous plant operations
AI is the highest level of maturity in Industry 4.0 adoption. While manufacturers have started to integrate traditional AI technologies such as machine learning (ML) into their processes, they are not realizing their goals: a study on AI integration found that less than 17% of organizations had achieved their AI adoption goals in 2023.
BASF implemented an Industry 4.0 solution to optimize the catalyst process for styrene, a liquid used to manufacture industrial products. ML is used to predict the optimal catalyst bed temperature and the selectivity of styrene under multiple operating conditions. The solution provides guidance to its customers for ongoing operations and catalyst life prediction.
Shell has taken steps toward autonomy in its operations. It has gathered 2.7 trillion rows of sensor data to monitor 10,000 pieces of equipment across its operating assets and enhanced operations using AI. This has helped Shell optimize its operations to match market conditions, maximize plant utilization, and prevent unplanned downtime. With an ambition toward semi-automated operation, autonomous inspection devices, like mobile robots and drones, are used to measure factors such as corrosion and emission levels.
AI has been evolving since that 2023 study, with generative AI being more widely adopted, and with businesses thinking more strategically about their use of it. According to the Infosys Generative AI Radar study, 48% of energy, mining, and utility enterprises have already implemented generative AI, or are in the process of doing so.
There are exciting use cases for generative AI: Professor Ramamoorthy Ramesh and his colleagues at the University of California, Berkeley use generative AI for new materials discovery. He and his colleagues are looking at 100 years’ worth of data to analyze and optimize material structures and processes.
“Many properties, whether it's electronic, structural, or magnetic, are very dependent on how the atoms are orbiting and we should be able to predict that,” using generative AI, says Prof. Ramesh. Generative AI can be used to try different atomic configurations at a microscopic level to determine their macro-level properties for each configuration and choose the best option.
Recommendations
- Maturity level assessment: Companies in process manufacturing should assess where they are in the Industry 4.0 maturity index framework. They should set a time-bound target of what higher level to achieve when and plan for the necessary investments required for the same. Autonomy cannot be achieved in one step but with increasing maturity in levels of digitization.
- Simulation before implementation: Simulation models should be built for decisions at all stages in a factory, from the design of a plant or asset to its installation, operation, maintenance and end-of-life management.
- Mapping stages to business objectives: The stages in the maturity of Industry 4.0 adoption and their basic tenets should be mapped to specific business objectives. That will ensure that digital technologies are not implemented solely for functionality but aligned to a company’s strategy with financial targets.
Efficiency, capacity utilization, and quality are crucial targets for the process manufacturing industry to achieve high returns on the capital employed. Industry 4.0 will play a key role to achieve these targets for both green field plants to be setup and for brown field plants undergoing digital transformation.
Industry 4.0 and its associated technologies will play a key role to achieve high return on capital employed in the process industry.
