Lessons from Software Agility for Sustainable Product Innovation
"In an agile project, technical excellence is measured by both capacities to deliver customer value today and create an adaptable product for tomorrow." – Jim Highsmith, author of Agile Project Management.
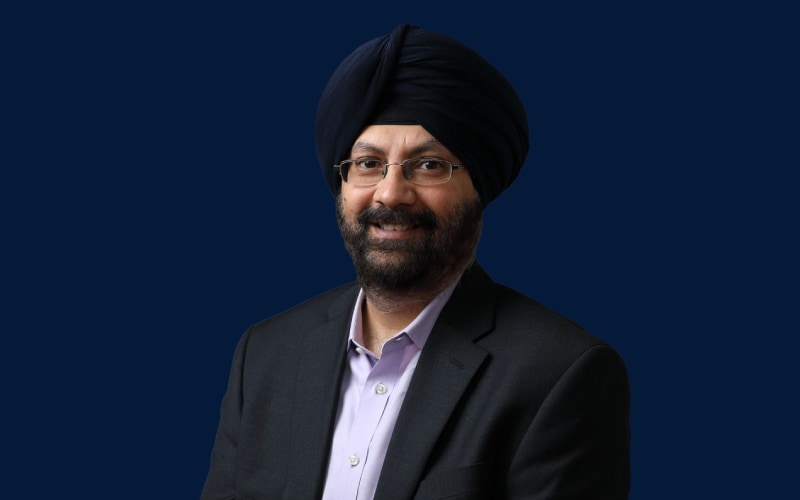
While the quote above refers to the practice of agile software delivery, I believe it is truly relevant for sustainable product development in a circular economy. In fact, I see that, over the years, there are several similarities between the evolution of software development and manufacturing, particularly when it comes to agility.
Traditionally, application development teams used the waterfall method. This is a phased process where one step (say testing) could only be executed when the previous step (development) was completed. The disadvantage was long turnaround times to the release of the software. And this was followed by lengthy cycles to push enhancements or upgrades. In cases where users reported issues after go-live, it led to a repetition of the process right from step 1 to final delivery. When the agile method was introduced, it made things faster and more intuitive by enabling continuous iterations where development and testing could run in parallel.
Let’s take two principles of agile software delivery – user feedback and faster enhancements – and compare them with circular economy.
In agile software development, constant feedback closes the loop. This is done by providing developers and testers with reviews on how the software works in real-life, whether it functions as it is supposed to and whether it is accessible. These teams then integrate the feedback by making adjustments to the code, thereby providing continuity and ongoing improvements. Moreover, new features and enhancements on existing code can be rapidly pushed to users, giving them better quality and increasing user delight.
In a circular economy, linear manufacturing processes (like the waterfall method) are being replaced by circular ones (like agile). Reverse logistics close the loop – just like user feedback. And, manufacturers who are able to innovatively reuse these products through refurbishment or recycling drive reusability – just like software upgrades and enhancements.
Agility in Circularity
Why is it important to be agile in a circular economy? Depleting natural resources are forcing manufacturers to take a closer look at how they produce what they produce. Sustainable production, from raw materials to reuse of old equipment, is becoming a global imperative. To minimize waste, the focus is shifting from simply manufacturing products to creating services from those products. Thus, manufacturers and consumers are jointly sharing the responsibility for creating and maintaining product longevity. Manufacturers are also increasingly collaborating with suppliers to discover green ways of sourcing. In the near future, they will re-configure their supply chains to encourage product return from consumers for greater reusability. And, they will infuse cross-functional expertise to find smarter and more sustainable solutions. Ultimately, this will lead to a slew of product innovations.
Take the case of Xerox. It incorporates circularity by making managed print services, not copiers, the heart of its business model. Its products are designed such that when these are returned, the scope of refurbishment and upgrading is much higher by, for instance, reducing the number of plastics from 500 to 50. Here, product design is not just for manufacturability but for maintenance, disassembly and upcycling.
In short: Customer value today, and an adaptable product for tomorrow.
All of these – servitization, collaboration, shared responsibility, and reusability – leverage the core principles of agility. And just as technologies like automation, cloud, data, and analytics enable agile software delivery, I believe these will have a crucial role to play in product innovation for agile manufacturing as well. For instance, Toyota uses Eco-VAS, a networked software tool, to measure environmental impact. This tool sets impact reduction targets and allows developers to track performance, CO2 emissions and fuel efficiency of its vehicles during the development process. Infosys, too, leverages robotic automation to optimize material movement and improve warehouse utilization as part of our logistics optimization solution, thereby reducing carbon footprints for automotive manufacturers.
Building circular communities
While these are examples of some manufacturers and technology companies trying to make a difference, the circular economy calls for a wider approach.
I think this might look a lot like the city of Shenzhen, China. Hailed as the world’s most innovative manufacturing hub, the city is governed by an ethos of collaboration and strong stakeholder engagement. Manufacturing in Shenzhen empowers start-ups to get their ideas to market faster and, often, cheaper. Instead of owning the intellectual properties of goods, producers use a kind of open source ideology where ideas are shared, resources are mobilized, and knowledge constantly improved on.
This shared ecosystem makes it ripe for agile manufacturers to evaluate whether they are delivering efficient and green products for their consumers today, which can be sustainably adapted for tomorrow. When manufacturers choose to work within the circular economy, each member of the ecosystem becomes responsible for ensuring their supply chains operate sustainably. From a local and global perspective, it creates whole communities and ecosystems thriving on the principles of reuse, remanufacturing and recycling. By coupling rapid product innovation and development (like in Shenzhen) with agile methods (like in software delivery), manufacturers can light the way for other industries on conservation and sustainability.