Success Stories
Know how Infosys helps its clients realize their business potential
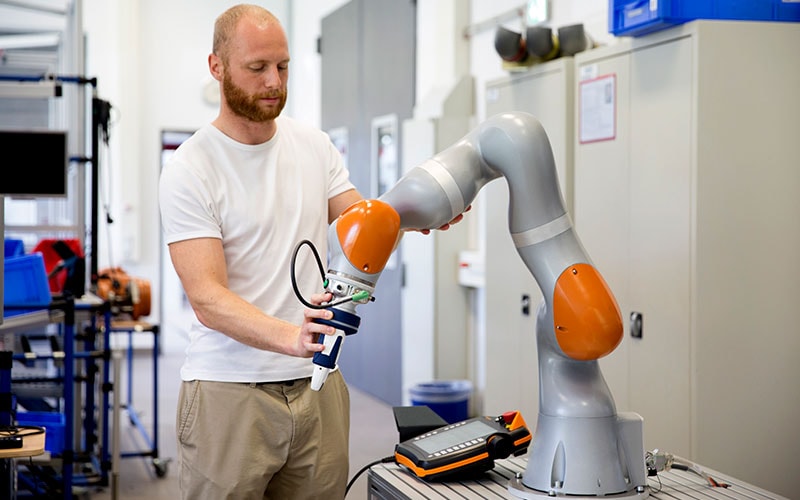
Case Study
Enterprises need resilient networks, digitally connected workforce, and smart connected products, to reorient their production to be more local and enable faster launch of new offerings. This requires massive engineering interventions in product design, software defined networking, robotics, IoT and containerization. Infosys Engineering Services is strategically positioned to respond to real-time customer needs and build technology offerings that are highly competitive while focusing on continuous cost improvements.
Here's what several independent industry analysts, experts and observers have to say.
Engrossing conversations with industry leaders and partners
Know how Infosys helps its clients realize their business potential
Case Study
Service Offerings
Business Solutions